Strict Quality Control to Create High-performance Sports Protective Gear
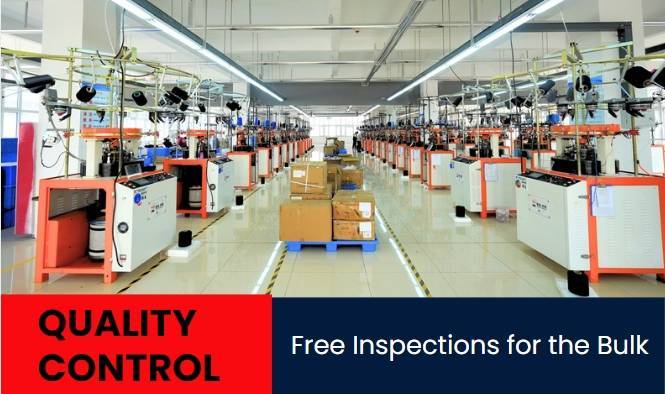
" China Sporting Goods Exhibitions Overview
1. The importance of high quality
2. Raw Material Quality Assurance
3. Quality control in the production
4. The Bulk Goods QC after Production
5. Finished product testing: multi-dimensional assessment of performance
6. Customer Feedback and Continuous Improvement
7. Summarize: the value of quality control to the supply chain and brand customers
1. The importance of high quality
In the highly competitive sports market, the consumers' requirements for sports protective gear have already gone beyond essential protection. They are looking for high-quality products with safety, comfort, durability, and these sports protective gears even can improve sports performance. This pursuit of high quality is not only due to the importance of their health but also a kind of trust in the brand.
Have you ever been worrried about the quality of your brand's sports protective gears? As a sports protective gear factory, we are well aware that product quality is the brand's lifeline. We are constantly pursuing how to achieve "high quality" and make every sports protective gear shipped become the brand's spokesperson.
2. Raw Material Quality Assurance
As a brand of sports protective gear, high-quality raw materials ensure excellent product performance, such as breathability, elasticity, wear resistance, etc., and provide consumers with a safe and comfortable sports experience. Especially for products that come into direct contact with the skin, such as knee supports and arm sleeves, the safety and comfort of the material are directly related to the end-user's experience and the brand's reputation. In the selection of suppliers, while stable supply is crucial, it is even more important to ensure that they can provide internationally certified safe materials.

Quality of raw materials
First of all, quality certification is one of the primary conditions to determine whether a raw material supplier meets the standards. Oeko-Tex certification is a globally recognized textile certification standard that ensures no harmful chemicals are used to produce the material. In order to ensure the quality of our products, we are extremely strict when selecting our raw material suppliers. They must be internationally certified, such as Oeko-Tex Standard 100, which proves that their raw materials meet the highest environmental standards. This is particularly important for customers in the European and American markets, where consumers have higher demands for safe and environmentally friendly products. In addition, we conduct regular site visits to our suppliers to learn about their production processes and quality control systems to ensure the stability and reliability of our cooperation.
Performance of raw materials
At the same time, we also need to pay more attention to functional performance of raw materials, which directly determines the performance of the finished products. Different sports protective gear has different functional requirements such as sun protection sleeves are made of UV sunscreen fabric. Breathability, moisture absorption and perspiration, antibacterial properties, and sun protection index are all important indicators to measure the quality of suppliers 'raw materials. Among them, materials with good breathability can help the skin keep dry during high-intensity sports, while antibacterial materials help prevent the growth of bacteria, thereby ensuring hygiene for long-term use. To evaluate these properties more objectively, we will send raw materials to third-party authoritative organizations for testing to obtain a more credible test report.
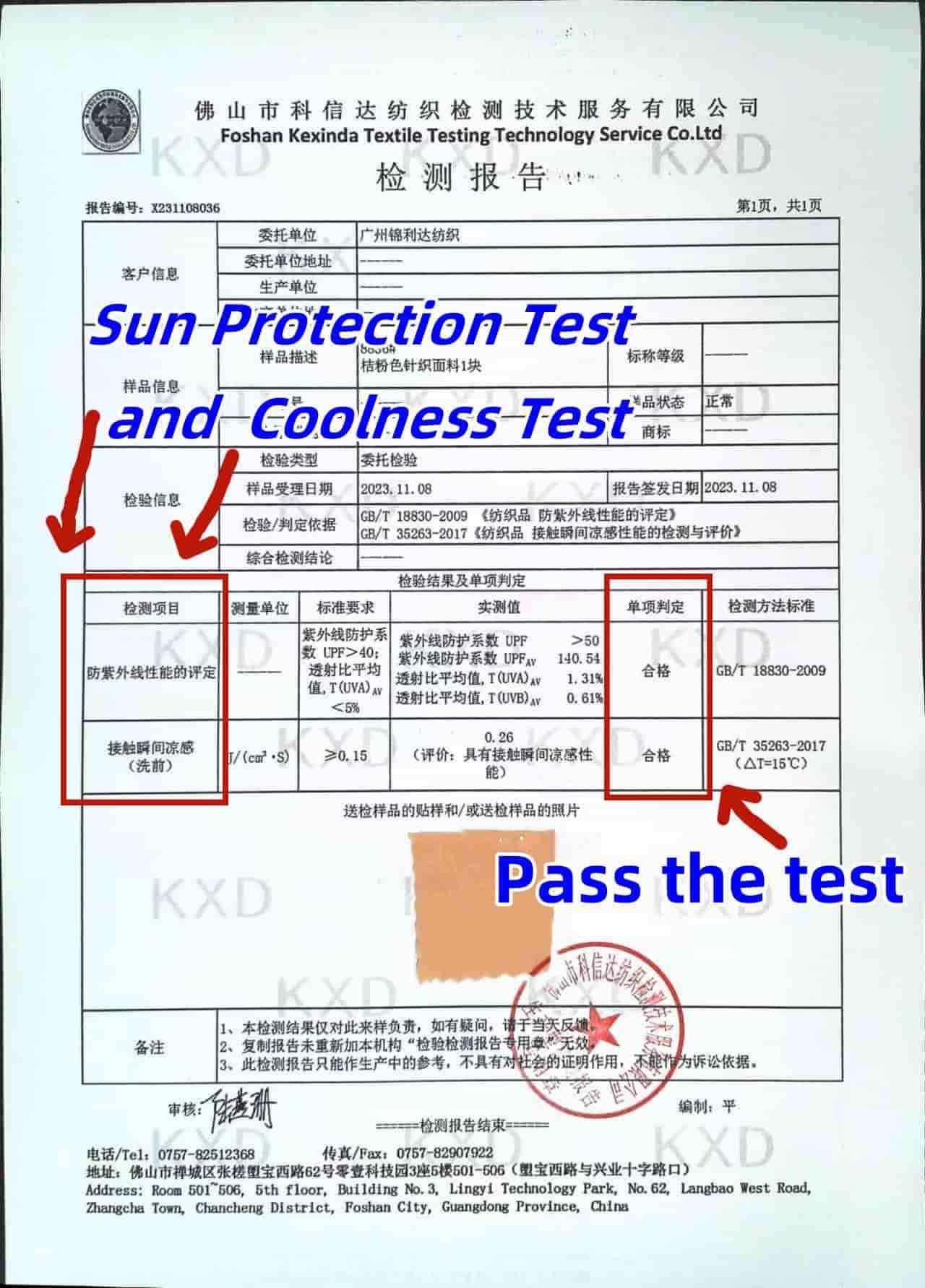
Environmental and sustainability
In the current global market, more and more brands and customers pay attention to environmentally friendly and sustainable development. Especially in the European and American markets, using environmentally friendly materials is helpful to improve brand image and become a key advantage in market competition. Adhering to the concept of sustainable development, sports protective gear manufacturers are not only practicing social responsibility but also winning over consumers by adopting sustainable and eco-friendly materials and optimizing production processes (minimizing negative impacts on the environment during the manufacturing process).
3. Quality control in the production
Automatic production
Our factory has advanced production and manufacturing equipment such as German MAYER&CIE knitting machines, Japanese SHIMA SEIKI SHIMA SEIKI-7G fully computerized knitting machines, cutting machines and high-frequency machines. These equipments can accurately control every production parameter to ensure that every detail of the products meets the design requirements, which provides a strong guarantee for the stability of product quality. We have more than 200 fully-automated production lines, and each process has a strict standardized workflow, which can effectively reduce human error. In addition, the fully automated production lines can not only greatly improve the production efficiency, but also quickly fulfill a large number of orders to meet the urgent needs of customers.
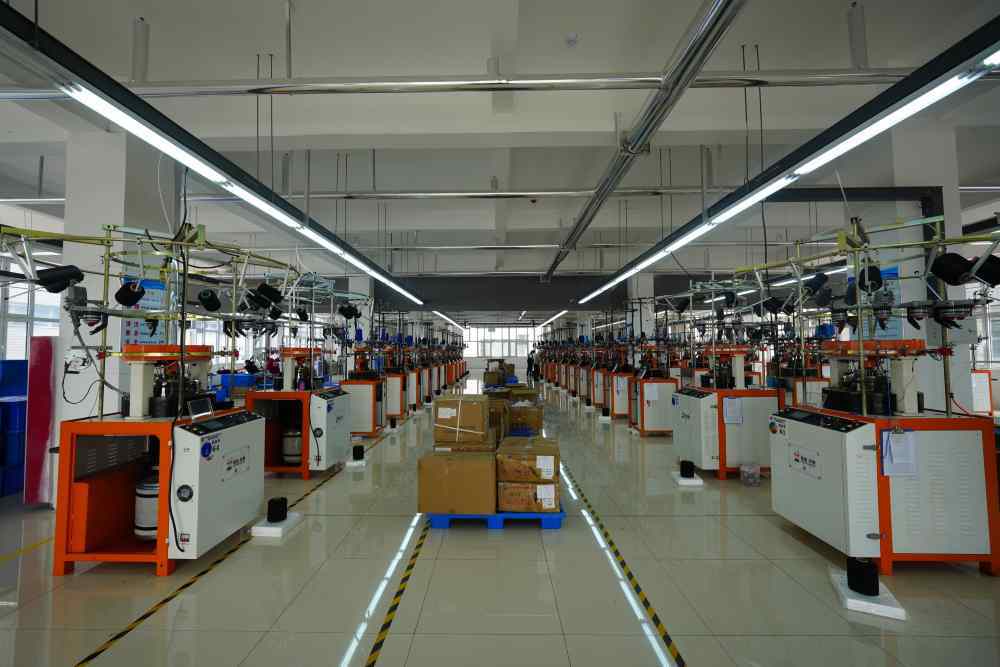
Process Quality Control
Process control QC plays a vital role in our sports protective gears production process. Setting up strict quality checkpoints at every production process ensures that every product meets high quality requirements. We have reserved a dedicated area for displaying defective knitted protective gear products, which are marked with quality errors one by one. This display area helps our team to continually learn and identify quality issues and ensure that our products meet the highest standards finally.
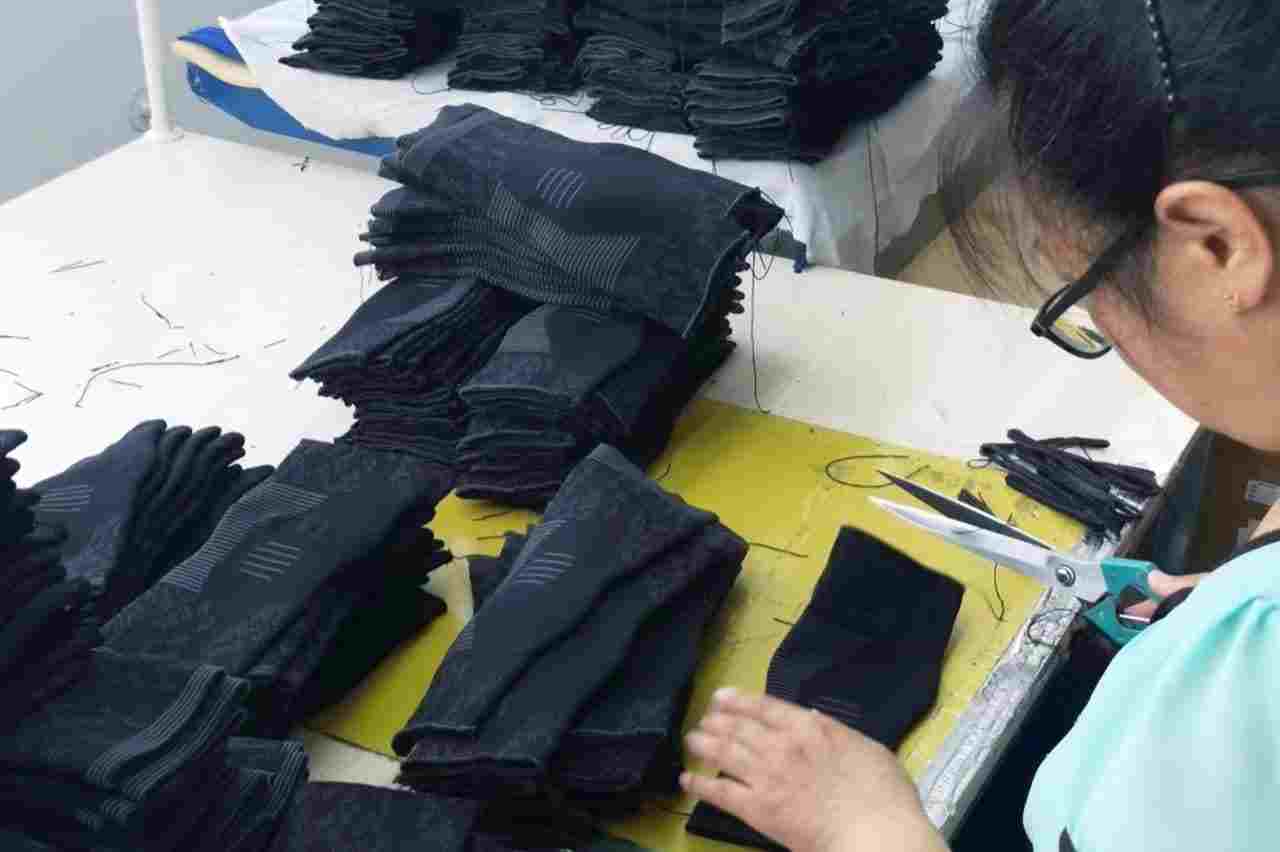
- Tailoring
It has two stages. One stage is to cut the raw material, such as waist and shoulder supports, which are sewn from fabrics and require advanced cutting equipment to lay out and cut large pieces of fabric to maximize the use of fabric, reduce material waste, and ensure accurate cutting size. Another stage is to handle the semi-finished products that come off the circular or flat machines, which usually come with many threads. Before proceeding to the sewing step, our workers will cut off excess threads and remove semi-finished products with defects such as stains and holes, thereby reducing the risk of returns and exchanges for customers.
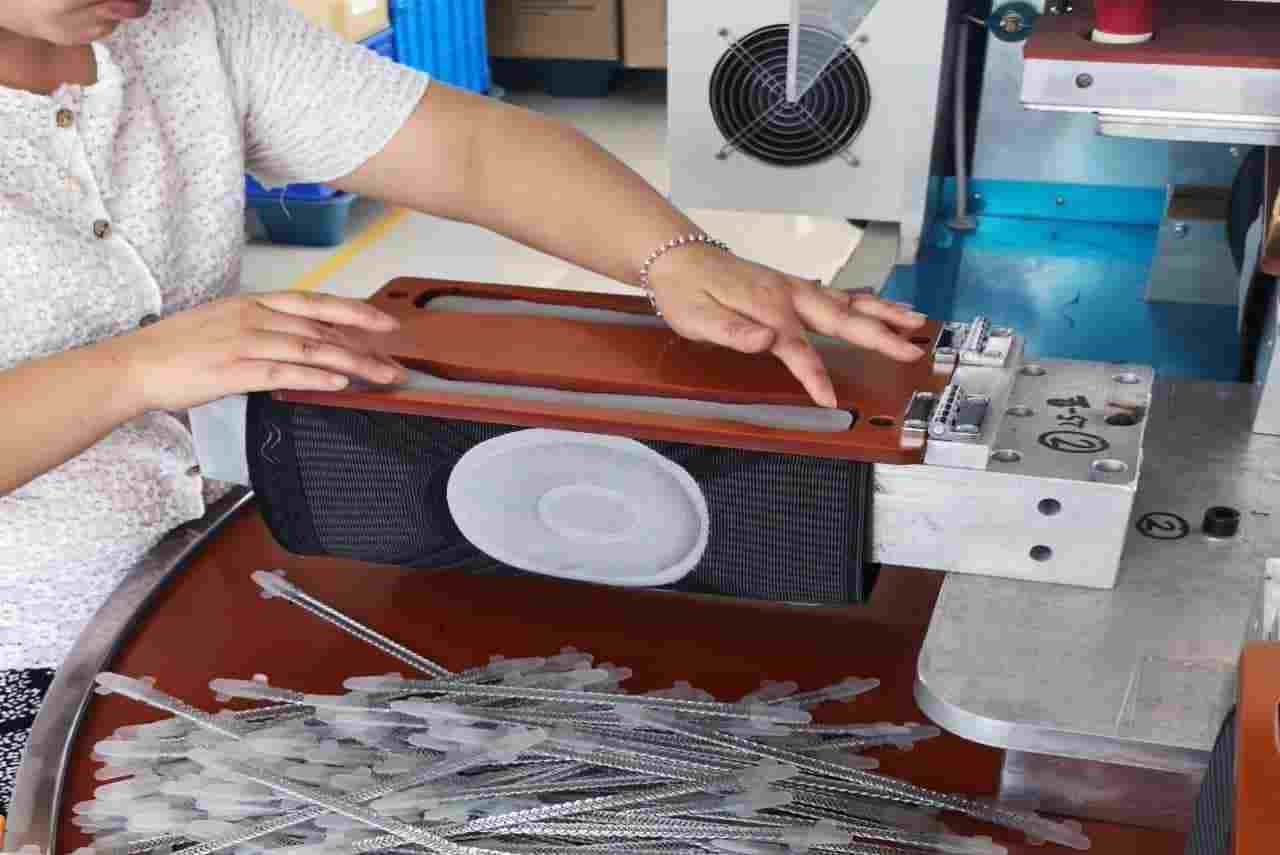
- Accessories and Sewing
For products that need to add functional accessories, we will strictly control quantity, and quality of the accessories before production. This ensures the semi-finished products can directly enter the next process when they are coming off the knitting machines, which can speed up the production. Immediately after the semi-finished products are produced, we will carry out the process of adding accessories, such as anti-slip strips on the rosette of the knee pads, sewing spring strips on the side of the knee pads, anti-collision shims or cushioning pads, and so on. In the subsequent sewing stage, we will do fine locking, marking, and hemming to ensure the seams are flat and firm, without wrinkles and crookedness.
The team in our processing workshop consists of experienced craftsmen who have been trained in professional craftsmanship and can skillfully complete all operations, greatly reducing the rate of product defects.
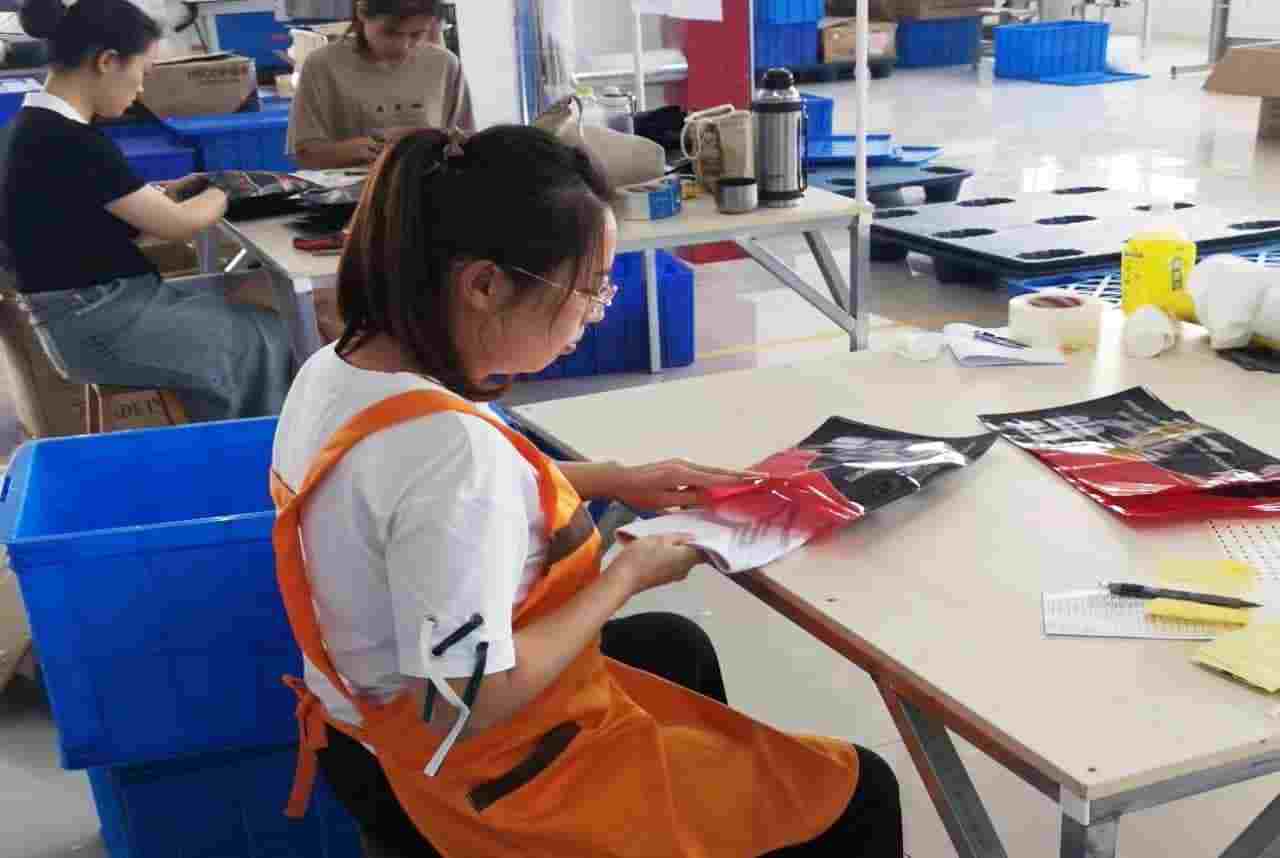
- Packaging
The packaging process varies depending on the different packaging style. The most common method is to place the product such as an ankle sleeve into an OPP bag and label the packaging with a size label and barcode. Before packaging, we will conduct a comprehensive visual inspection of each product to ensure that there are no flaws such as damage, stains, and threads. During the packaging process, we check the product's size, specifications and other information to ensure that they are consistent with the order information. For pairs of sports protective gears (such as compression arm sleeves and knee supports), we pair them strictly in accordance with the order requirements to ensure that the size and style of the left and right feet or hands are consistent. Then, recheck the size of the product to ensure that it is consistent with the order information and avoid returns caused by size errors. We also ensure that the quality and size of packaging materials meet customer requirements.
4. The Bulk Goods QC after Production
Customer satisfaction has always been our pursuit. In the bulk QC, we uphold stringent quality standards to ensure that each batch of products can be delivered perfectly. Our product pass rate is 99.8%, far exceeding the industry average. Next, we will introduce our factory's own QC process for the bulk and our support and assistance we can provide in third-party inspection.
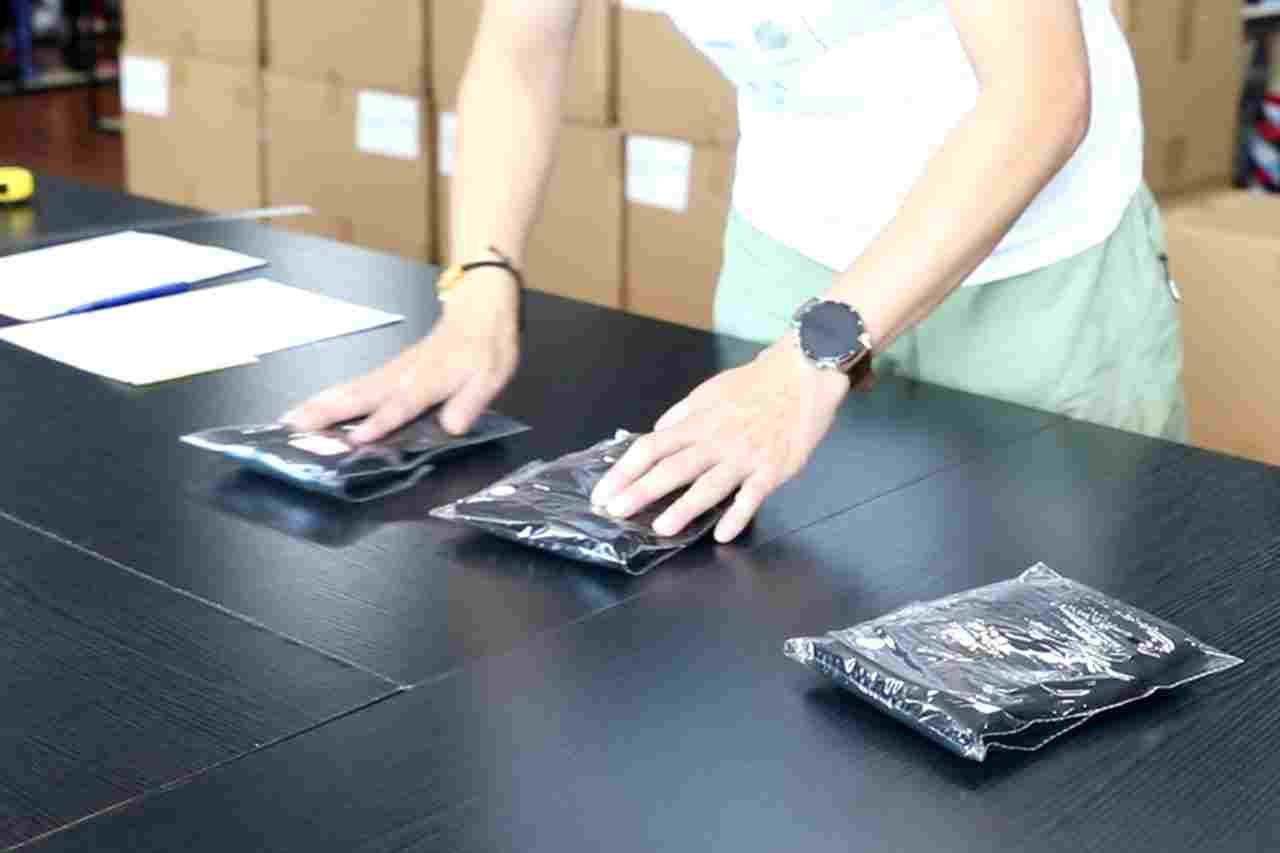
Sampling inspection of finished products
Barcode Scanning: Each shipment is barcode scanned after packaging to ensure that the barcode information is consistent with the product information, and UPC barcodes are critical in inventory management. We perform a final quality inspections on each shipment, scanning the barcodes to ensure the products are accurately identified when they arrive at your warehouse. This process can significantly reduce the risk of logistical errors and improves overall operational efficiency.
AQL Sampling Inspection: Before shipment, we will conduct sampling inspection on packed products according to AQL standards to ensure that the product quality and packaging quality are in line with customer requirements and international standards. In order to ensure the randomness and representativeness of sampling detection, our quality control team will make a sampling plan according to each batch's specific situation. And each inspection undergoes a rigorous process that complies with AQL sampling ratios and defect control limits. This ensures the quality of shipments and provides customers with a higher sense of security and trust. We keep detailed records of the inspection results and set up a feedback mechanism to adjust the production process in time to optimize product quality.
Logistic information checking: We will check the logistic information before shipment carefully such as shipping paper, to ensure that the products can be delivered to customers accurately. In addition, we kept close communication with logistics companies to ensure that goods are effectively tracked during the transportation process, allowing our customers to check the transportation status of their goods at any time, thus further enhancing their trust and satisfaction with our services.
In addition, we offer a flexible inspection process that can be arranged at different stages of production according to customer needs, to ensure that every step of the process meets quality requirements. We follow internationally recognized standards to ensure product quality meets customer expectations. These include AQL standards, which determine the number of samples to be sampled and the pass rate according to customer requirements; ISO 9001 quality management system, which ensures that the production process and quality control are in line with international standards; and inspection standards based on customer-specific requirements. Through these quality standards, we try our best to provide our customers with high-quality products. Upon inspection completion, we will provide our customers with a detailed inspection report, including test items, test results, and pictures. If any defective products are detected, we will replace them to ensure the quality before shipment.
Third party inspection
We welcome third-party inspection to show our customers the high quality of our products in a transparent. We can provide the convenience for the third-party inspection organization, including providing production information and samples and arranging an on-site inspection.
The inspection process includes:
• Making an appointment for inspection.
• Preparing relevant production data.
• Providing samples.
• Arranging an on-site inspection.
Customers or inspection organizations need to contact us in advance to determine the inspection time. We will prepare the production materials and samples in advance. Upon arrival, the inspection personnel will check the product's appearance, size, material, and function according to the agreed standards directly. After inspection, the third-party organization will issue a detailed inspection report describing the findings and recommendations.
5. Finished product testing: multi-dimensional assessment of performance
Our factory has purchased imported R&D testing equipment and is the first compression-type protective gear testing center in China. In order to ensure that our sports protective gear can withstand the test of high-intensity sports, we will conduct strict tests on the finished products. These tests include durability tests that simulate real sports scenarios, such as stretching and friction tests. In addition, we also focus on functional tests to ensure that the protective gear meets the performance requirements. For example, through fitting tests, we continue to optimize the comfort of the knitted sports protective gear so that the wearer can be more comfortable during exercise. Through these tests, we can continually improve the quality of our products to meet the high standards that our customers demand from their sports protective gear. We can provide relevant data and reports if required.
Durability test: The durability test is a key part of evaluating the performance of protective gear under high-intensity use. We simulate extreme sports scenarios and test the tensile length and sewing fastness of the knee pads and arm sleeves to ensure that the products will not have quality problems in actual use. The test items also include color fastness, tensile strength, etc., to ensure that each can maintain good condition during long-term high-intensity sports and effectively protect the safety of athletes.
Functionality test: The functionality test is designed to verify that the design of the protective gear meets its intended function. For example, we conduct pressure value tests for compression arm sleeves to ensure that their support meets the design criteria and customer requirements. In addition, we test the water absorption and sun protection properties to ensure that athletes are adequately protected in all environments. These functionality tests help us find potential problems before the product is released to the market and ensure each piece of sports protective gear can be used safely when they reaches the customers.
Comfort Evaluation: Comfort evaluation is an important part of ensuring that athletes do not feel uncomfortable when wearing protective gear for long periods. We collect feedback from athletes through fitting tests to evaluate the protective gear's fit, breathability, flexibility and etc. By constantly adjust, we strive to provide the best wearing experience while maintaining functionality. This improves the comfort and the sports performance of the athlete in real sports, allowing them to be more comfortable in intense competitions.
6. Customer Feedback and Continuous Improvement
Customer feedback is an important basis for our continuous improvement. We regularly collect customers' opinions and suggestions through multiple channels, including online surveys, customer interviews, after-sales service feedback, etc., to ensure know as much as possible about our customers' needs and opinions, and continuously optimize our production and inspection processes based on these feedbacks. In order to ensure closed-loop management of feedback information, we have set up a special customer service team responsible for collecting and sorting feedback information, promptly following up the progress of feedback processing, and feeding back improvement results to customers. In this way, we are not only able to maintain high quality standards for our protective gear products, but also continue to improve customer satisfaction and enhance customer trust and loyalty.
In addition, we regularly conduct customer satisfaction surveys to assess the level of customer satisfaction with our products and services through a specific rating system. The survey results will directly influence our decisions and help us identify key issues and customer concerns. By analyzing feedback data, formulating targeted improvement measures, and conducting reports and discussions within the company to ensure that each department can understand customer needs. Such surveys not only provide us with a direction for improvement, but also allow customers to see that their opinions are valued, which promotes higher customer satisfaction and stronger relationships.
7. Summarize: the value of quality control to the supply chain and brand customers
Quality control is not only a management tool within the factory but also the basis for providing stable and reliable products for brand customers. Through strict quality control, we can offer brand customers with high-performance sports protective gear and help them establish a good brand reputation in the market. At the same time, this efficient quality control system also improves the overall efficiency of the supply chain and ensures that our products remain competitive in a rapidly changing market.
Our factory is always committed to continuous investment and improvement in quality control to meet the changing needs of our customers. If you want to know more about our factory, click here to learn to view the factory introduction, explore our high-quality sports protective gear, click here to see more information about all custom knitted protective gear products , click here to see our custom compression arm sleeves products.